AFTER-SALES SERVICE
Committed to providing integrated, efficient and professional new energy, clean energy and distributed energy-based comprehensive energy solutions
- After Sales Team
- Service Operations
Efficient after-sales installation and commissioning
Safe lifting and positioning of equipment
quality control of concealed construction
On-site pre-burial and reservation
Confirmation of piping connection location
Reasonable positioning and fixing of the unit
Equipment Entry Protection Alert
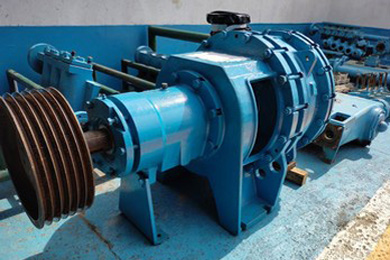
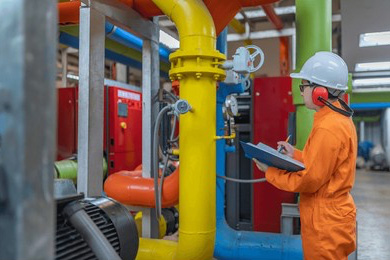
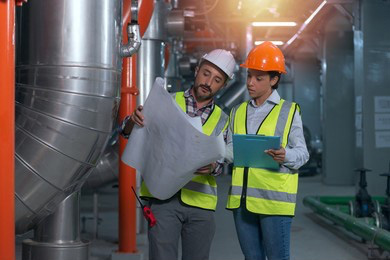
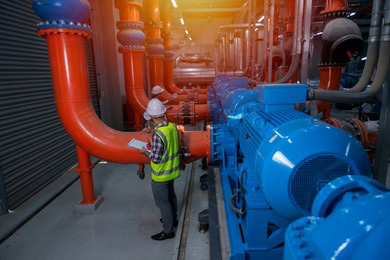
Standard Engineering Commissioning Process of AXXEN energies
Equipment installation inspection
Control parameter setting
Engine start up
Media fill required for operation
Insulation Troubleshooting
Startup checking and optimization
Functional testing of systems
Pre-commencement review
Commissioning report preparation
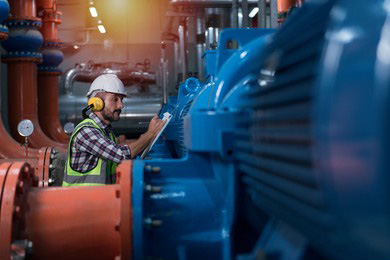
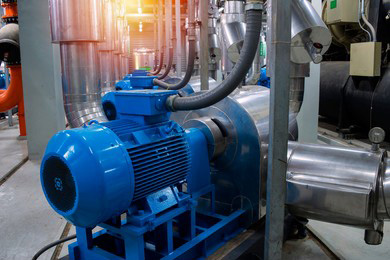
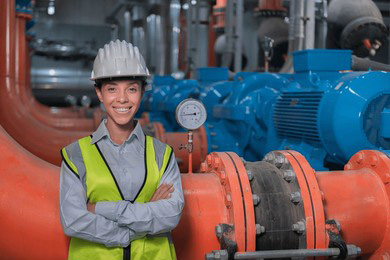
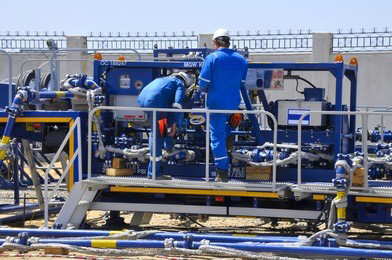
Five-star maintenance workshop
AXXEN energies technicians are rigorously trained in accordance with standards and latest specialized technical knowledge. Each technician follows standard procedures and professional requirements from basic disassembly, cleaning, assembly to testing. After the technician's perfect refurbishment, the machines and equipment can reach the same performance as new machines, and put into the second cycle of life. We have a well-equipped five-star repair shop, providing repair and complete overhaul services for all machines and spare parts. Engine repair differentiated services:
Full cleaning of the entire machine before entering the workshop
Use specialized equipment to clean and remove all aspects of each engine that will come into the shop so as not to contaminate the shop or the machines that are running.
Thorough disassembly and cleaning
Each part of the engine is disassembled one by one, thoroughly, and the parts are cleaned and de-painted using specialized equipment. All disassembled parts will be sorted and placed in order to prevent misplaced and lost parts, or even the occurrence of a multiplicity of sites.
Detection and repair
After the parts are cleaned, they are inspected by specialized technicians, repaired and assembled according to AXXEN energies specifications and processes.
Trial run
Restored engines must undergo power testing with state-of-the-art equipment to ensure that every engine restored is returned to the performance and standards of a new machine.
Customer Service Satisfaction Program
In order to improve customer satisfaction and service quality, after the end of the service will be a specialized staff to make a return visit to the repair work, and follow up on the customer's suggestions and complaints. And as the staff's performance appraisal index. Monthly meetings are held to discuss and summarize the results of the return visit.
S.O.S Oil Sample Inspection
AXXEN energies has one of the few fully-equipped, highly specialised oil sampling laboratories in the Asia-Pacific region. The laboratory is fully automated, computerised and monitored 24 hours a day, 7 days a week for accurate and efficient data processing.
Oil sample laboratory equipment: Inductively Coupled Plasma Spectrometer (ICP), Fourier Transform Infrared Spectrometer (FTIR), gas chromatograph spectrometer, viscometer, pH agent+conductivity+refractometer, oscillator, fume hood, diluter, oxygen/air generator, reagent cabinet, Specialized hot plate, Specialized balance, etc.
Genuine Axxen Energia spare parts
In order to ensure the normal operation of the equipment, AXXEN energies has established a complete set of global spare parts supply system, equipped with maintenance personnel and commonly used maintenance parts, to ensure that the user parts supply service, reduce the owner's operating costs. AXXEN energies has spare parts warehouses in each region, providing sufficient stock of genuine spare parts, all the warehouses are computerised management, which can provide customers with fast and efficient spare parts supply service.
Operation & Maintenance Management
The AXXEN Energies Machinery Service Center provides professional operation & maintenance management services.
By strengthening operation management, optimizing the operation mode of system equipment, strengthening maintenance management, and improving equipment availability, safety and economy, we can thus achieve lower operating costs and higher economic benefits for our customers.
-
Daily duty rounds and inspections
Performs walk-through inspections of equipment;
-
Develop a scientific maintenance program
Check and analyze the operating condition, working performance and wear and aging degree of the equipment, fully understand the changes in the technical condition of the equipment and the wear and aging situation, and provide customers with scientific maintenance plans for the problems found;
-
Regular maintenance
Perform regular maintenance on equipment according to the maintenance schedule
-
Fault treatment
After encountering a fault or getting a fault notification, immediately rushing to the fault site, communicating and negotiating with the customer's on-site management and technical personnel, and quickly and correctly handling the situation. Limit the development of the fault, eliminate the root cause of the fault, and remove the danger to people and equipment. As far as possible to keep the equipment continue to operate to ensure normal power supply.
Operations & Customer Service Agreement
AXXEN energies contracts with its customers to provide periodic maintenance services, S.O.S. fluid testing, and equipment walk-through inspections of the customer's equipment in order to keep the equipment running at peak performance and to reduce the risk, cost, equipment disruption, and damage caused by unforeseen equipment downtime.
-
Full service maintenance check
By professional maintenance engineers to provide a yearly formal maintenance and four comprehensive and systematic inspection (inspection frequency can be separately formulated according to customer requirements), timely detection and treatment of hidden equipment, improve the reliability and safety of the equipment.
-
S.O.S Oil and fluid testing
Provide 5 times a year oil sample testing (the frequency of inspection can be separately formulated according to the requirements of the customer), after the oil sample analysis equipment and technology of Essen Energy Cash to analyze the engine lubricating oil and coolant, in order to understand the wear condition of the internal equipment and the use of coolant. We analyze the engine lubricating oil and coolant to understand the wear condition and coolant usage inside the equipment, and to find out the potential faults and do the maintenance before the fault.
-
Emergency response time
24-hour online service, and after receiving the repair call within 2 hours to make the corresponding, priority dispatch and in the normal working hours of 12 hours to arrive at the scene for maintenance (the specific time is distance dependent), in order to reduce customer losses caused by equipment failure.
-
Discounted prices on spare parts
Pure original parts supply, special contract customer spare parts discount, not affected by the annual price increase factor; spare parts within the warranty period and meet the relevant conditions of the claim, without the need for the contract customer to bear.
Warranty Service Extension - ESC
The AXXEN Energies engine has a comprehensive global warranty system. In addition to enjoying the warranty of the newly purchased engine, customers can also purchase the Extended Warranty from the AXXEN Energies agent, which solves all of your worries.
Warranty Extension Advantage:
- 1. Avoid unforeseen costs due to unplanned maintenance
- 2. Using original Essen Energy parts, and trained technicians to carry out repairs to minimize downtime.
- 3. Multiple plan options to choose from to easily meet your business needs
- 4. Regardless of whether you are the original owner of the equipment or non-original owner, regardless of whether you hold a new or old machine, your equipment can enjoy the Essen Energy to bring you value-added services ---- extended warranty!
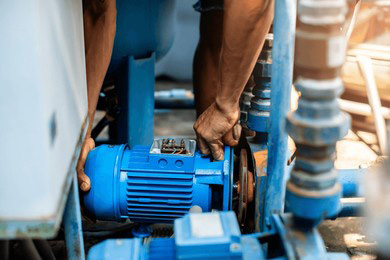
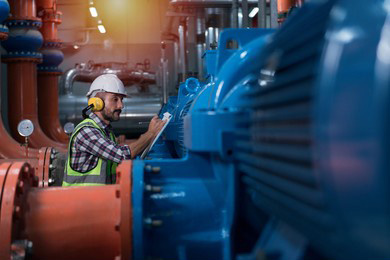
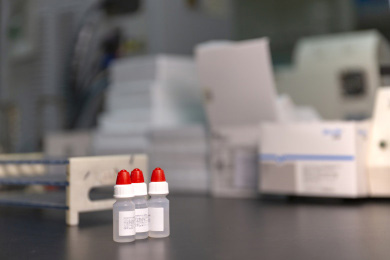
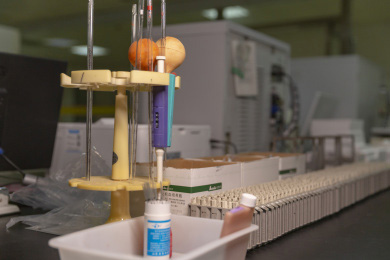
Complete customer training system
Axxen Energies has a specialized customer training center. Within the 500 square meter training space, there is a Hands-on training area equipped with a library of technical information, testing tools and other training aids (including engines, major parts, etc.).
AXXEN Energies regularly conducts customer after-sales exercises to help customers understand the knowledge required for proper operation and maintenance. The presentations include training on engine operation and basic proper maintenance techniques to enable customers to manage their engine equipment properly and increase its service life, thereby increasing productivity.